The USC Department of Mechanical Engineering's faculty and students are stepping up to support hospitals during the COVID-19 pandemic. Through a collection of personal and university-owned 3D printers, the team is manufacturing face shields for hospital workers to use as protection against the virus.
The project began with Robin James, a Ph.D. candidate in the department, and Sowmya Raghu, a research associate and adjunct instructor. They reached out to Jamil Khan, the chair of the department, and got in contact with Austin Downey, the faculty member for this project.
“I really liked the idea mainly because they were working with a few different hospitals to try to find a design that hospitals would take,” Downey said.
The Medical University of South Carolina (MUSC) contacted Raghu through a 3D printing forum to inquire about a team from USC making face shields for them.
Most hospitals are not willing to take homemade respirators and face masks.
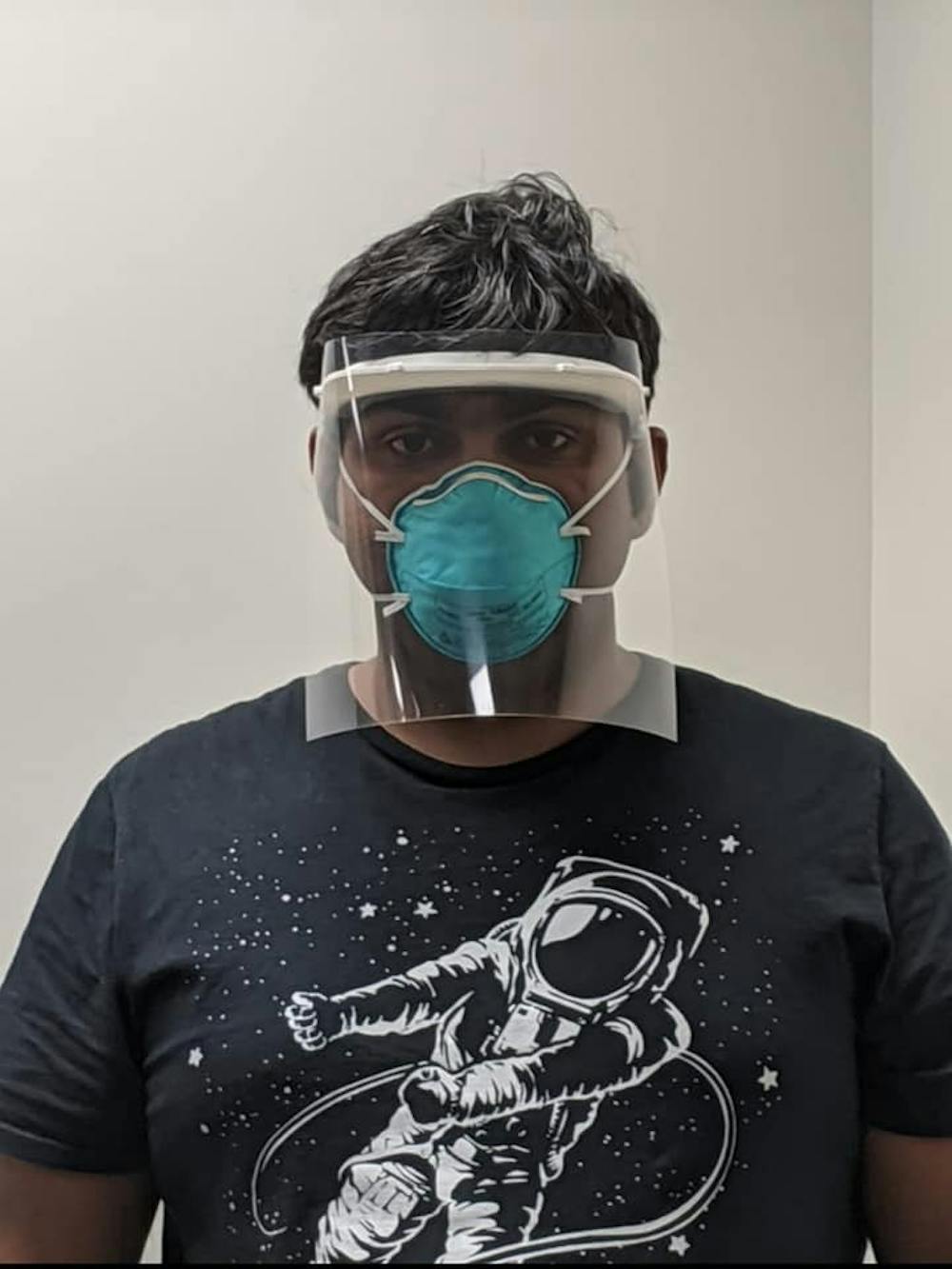
Currently, the team is made up of 15 volunteer faculty members and students who are working the printers from garages, living rooms and bedrooms. They have a total of eight printers that came from personal collections and classrooms. An order for more printers has just been placed.
"We've been working really hard on the last week, [but] this is really led by Robin and Sowmya," Downey says.
The team members planned to ship out 500 face shields by April 4 but ended up surpassing their goal, making about 600.
"Manufacturing and assembling the number of shields that we had in mind was a great collaborative effort of many students and faculty who took it upon themselves to 3D print these face shield from home," James said in an email interview.
The team has access to one of the engineering buildings on USC's campus to help them make the shields.
"That's how we finished our assembly for the first hundred," Raghu said.
They made 102 face shields by March 29, which will be sent to MUSC in Charleston. Their goal for the upcoming week, April 5 to 11, is to make more than 750 face shields, James said.
Downey and Khan said MUSC will eventually pay the team back for the project, but until then, the Department of Mechanical Engineering is spending money on supplies.
The team plans to continue this effort until the pandemic is effectively controlled.
"We are grateful to student volunteers who took time out of their busy schedule of attending online classes and conducting research remotely, to come and aid us in assembling these face shields," James said.
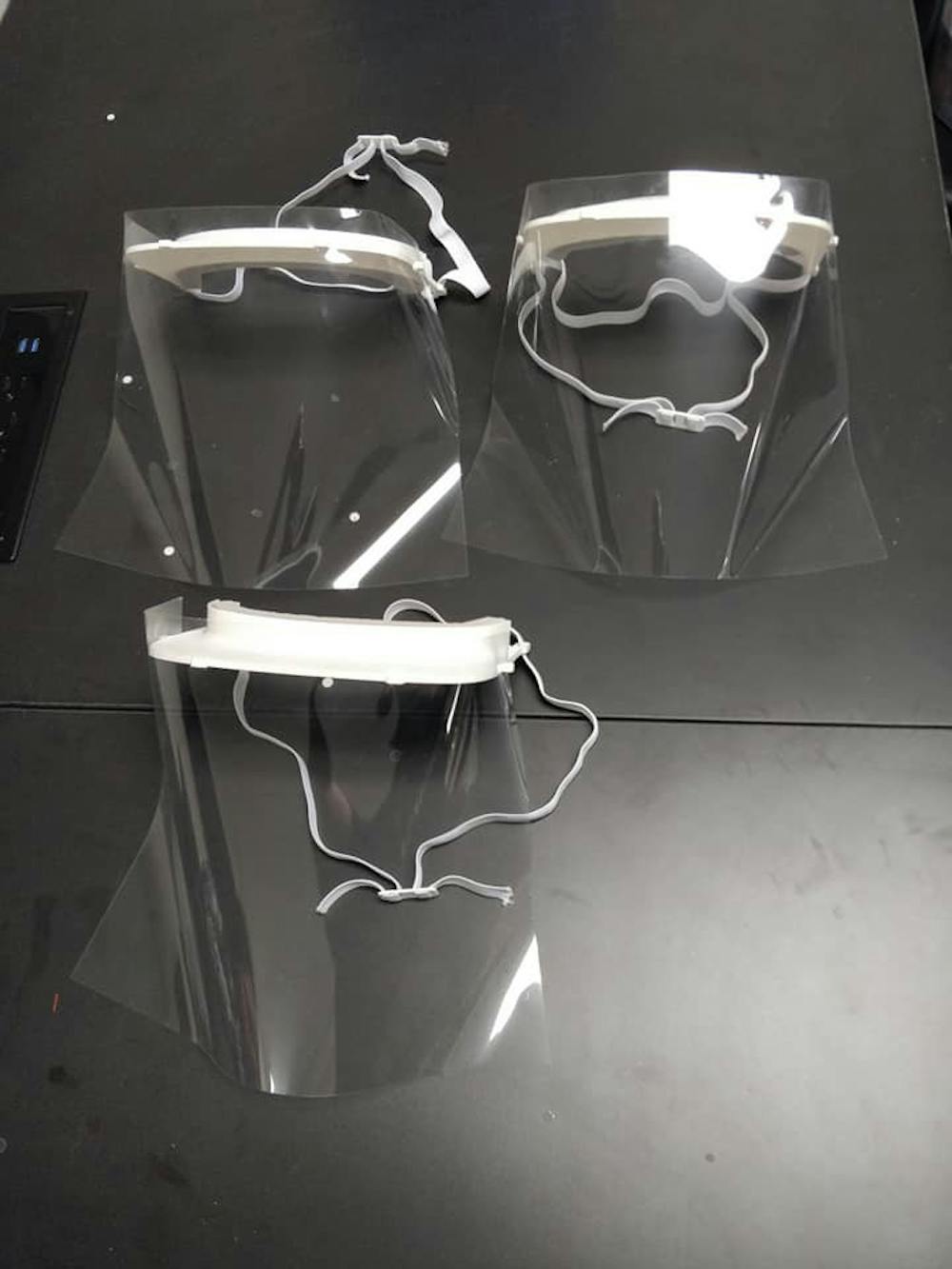
The face shields are made up of three parts: the headpiece, the shield and the elastic band. The headpiece is the only part manufactured by the 3D printer. The elastic bands are adjustable to any head size.
Many universities are also creating face shields, but Downey notes a lot of these projects have no scaling capacities and are only making one or two.
“That’s what’s different about this project [versus] a lot of other projects that you’re going to see,” Downey said. “Every university is and should have someone who is doing this.”